
类别:公司新闻 发布时间:2022-10-19 09:58 浏览: 次
日本电产的流体动力轴承原创设计优化工具
在日本电产,我们在设计风扇和鼓风机模块时利用超级计算机的计算能力来分析气流。此外,我们使用流体动力轴承的电机是在内部开发的分析软件的帮助下设计的。
当我们在 1990 年代开始奠定 CAE 技术的基础时,超级计算机非常昂贵。尽管如此,迈出计算机辅助工程的第一步对于为我们的新型流体动力轴承寻找最佳设计至关重要。
日本电产于 1994 年开始批量生产带有流体动力轴承的 HDD 主轴电机,NIDEC电机,并在 2000 年左右开始大幅扩大产品阵容和产量。随着使用流体动力轴承的模型数量增加,我们最初的设计方法——使用原型开发初始设计、执行测试然后反复微调设计——变得不切实际。随着产量急剧增加,从每月数万件到数十万件再到数百万件,以 ppm 数量级管理的质量控制变成了必需品,我们依靠有限数量的原型来检测有缺陷的设计的日子已经一去不复返了。
可靠地检测不遵循正态分布的异常值将需要超过一千个原型,并且从成本和交付时间的角度来看是非常令人望而却步的。因此,为了找到替代解决方案,我们着手开发一种方法——使用 CAE 技术——这将允许我们的每个设计工程师在他们的办公桌上分析产品设计。
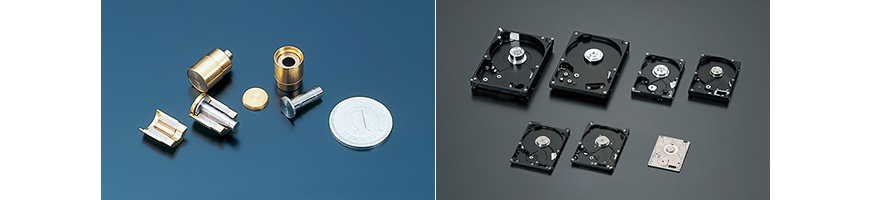
当时,商业上可用的分析软件工具对于我们的目的来说太慢了,因此有必要在内部开发新的软件。为了充分利用手头有限的计算能力,我们设计了一个专门的系统,汇集了分析流体动力轴承所需的所有功能。通过在二维中重新定义 3D 模型并将振动数据量化为许多离散的预定义模式,我们设法创建了一个有效的模拟工具,其范围缩小到仅包含与设计评估过程相关的现象。
流体动力轴承的内部衬有人字形凹槽,当轴承内部的轴旋转时,这些凹槽会在油中产生动态压力。在分析旋转过程中发生的振动时,轴承内部的线圈和阻尼器被隔离并用作轴和轴承的简化表示,从而更容易计算刚度和衰减。作为这些优化措施的结果,可以在 30-60 分钟内分析多达 1000-2000 个设计排列。
通过这种方式,我们能够快速计算出数千种模式,从而使我们能够以物理原型无法实现的规模检测和避免缺陷设计。
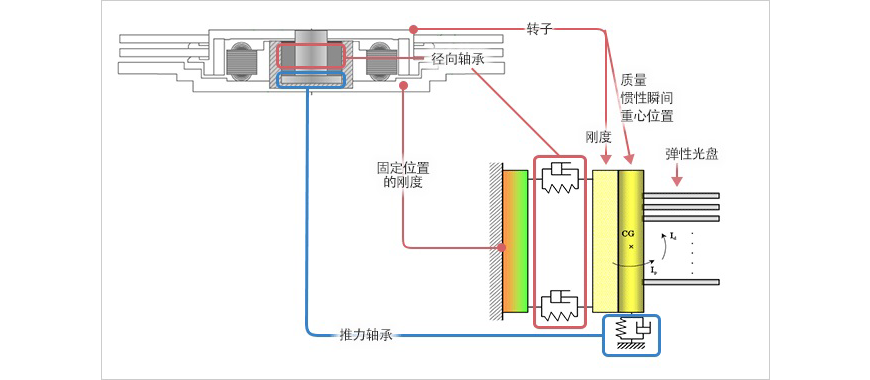
日本电产的分析软件开发团队与我们的设计团队属于同一部门。这两个团队每天都密切合作,开发现有软件工具的新版本以及全新的工具。超出我们软件开发团队能力的特别困难的项目,可以通过与我们位于日本川崎的新的最先进的研发中心合作来处理。
最近,我们扩大了流体动力轴承的使用范围,包括风扇电机。冷却风扇的设计需要使用流动分析,包括分析气流的行为和被风扇冷却的设备外壳内的热量分布。对于这些情况,我们利用超级计算机来生成高级模型并执行大规模计算。
除了我们与组件设计相关的专业知识外,Nidec 的设计能力现在还包括模块/单元以及安装我们模块和单元的最终产品的结构优化。以我们多年积累的独创CAE技术为后盾,我们努力超越仅仅成为您的供应商,而是成为您的合作伙伴。
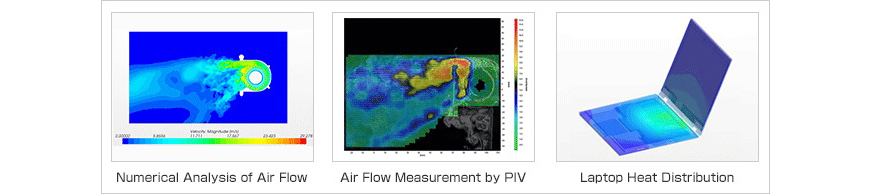